2022-06-28 | NYSE:DDD | Press release
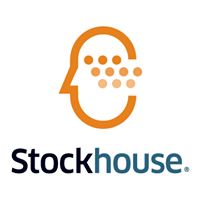
- Leveraging combined expertise to introduce DuraForm® PAx Natural – a first-to-market material available for all Selective Laser Sintering platforms
- Low cost, highly recyclable nylon copolymer designed for parts that withstand high impact and high elongation for a variety of industrial applications
- Low operating temperature reduces part pick-up time compared to other available nylon materials and increases printer uptime
ROCK HILL, SC and DOMAT/EMS, Switzerland, June 28, 2022 (GLOBE NEWSWIRE) — Today, 3D systems (NYSE:DDD) and EMS GRILTECH (SIX:EMSN) announced that it has entered into a strategic partnership to enhance the development of additive manufacturing materials. Combination of 3D&CloseCurlyQuote systems; expertise and leadership as an additive manufacturing solution partner with EMS-GRILTECH (a business unit of EMS Group) expertise in specialized polyamide manufacturing has enabled companies to introduce a new nylon copolymer – DuraForm® natural pax. This material has properties similar to injection molded plastics and exhibits high impact strength with high elongation at break in all directions. DuraForm PAx Natural is designed for use with any commercially available selective laser sintering (SLS) printer, regardless of manufacturer, making it easy to integrate into existing workflows.
3D Systems is the exclusive distributor of this material which can be used to fabricate strong, lightweight, production quality parts for applications such as orthoses, tool handles, splints and splints, ducts in environments tough, live hinges, fluid reservoirs and housings. requiring high impact and high toughness. DuraForm PAx Natural is designed to print at low temperatures (i.e. 120°C), which facilitates efficient printing and post-processing. Compared to other nylon materials (i.e. PA-11 and PA-12), DuraForm PAx Natural significantly reduces part preparation time, which not only helps service offices and manufacturers to maintain their competitiveness, but also helps to speed up supply chains. The low printing temperature of this material allows for high throughput and its designation as a clean working material results in reduced operator maintenance. With the lower printing temperature, parts can be ready to ship the day after an order is received. Similar PA12 based parts will need another day before a part is ready to ship.
DuraForm PAx Natural has very impressive long-term stability ratings of over five years indoors for mechanical properties and color. When parts are post-cured using steam lapping, finished parts have excellent translucency and a smooth finish which enhances the range of applications for which this material can be used. Additionally, the steam-softened DuraForm PAx Natural material moves the elongation at yield capacity beyond that of PA-11 and PA-12 materials. This material also has high reusability rates (a refresh rate of 30% is recommended), which helps reduce waste and lower production costs.
“We are very pleased to be able to collaborate with EMS-GRILTECH in a way that not only allows us to advance our innovation roadmap, but also advances the performance of materials for the industry,” said Dr. Edwin Hortelano, senior vice president, materials engineering and development, 3D Systems. “With DuraForm PAx Natural, we are not only delivering a superior product with state-of-the-art mechanical properties, we are also delivering a new material for use with any SLS printing technology, which we intend to expand to other powder bed fusion platforms. This is our first step in opening up 3D Systems’ materials portfolio to the entire industry, enabling more manufacturers to enjoy the benefits of this unparalleled material. We look forward to introducing more materials based on PAx and others in the future.”
Simon Maier, Head of Sales and Marketing at EMS-GRILTECH, said: “The EMS Group is an established global leader in high performance polymers for injection molding and powder-based applications. EMS-GRILTECH has watched the powder bed fusion (PBF) additive manufacturing industry with keen interest over the past few years, realizing that the technology is limited by the performance of available materials. So, with 3D Systems, we decided to use our expertise to develop materials that exhibit excellent performance in PBF systems and at the same time exhibit technical properties that match those of injection molding. EMS-GRILTECH is excited about the capabilities of DuraForm PAx Natural and we look forward to creating added value for the additive manufacturing industry with more new material releases in the future.
Although recently introduced, DuraForm PAx Natural is already receiving positive feedback from end users. “DuraForm PAx Natural fundamentally disrupts the cost structure of SLS technology and allows us to cost-effectively produce parts that were previously difficult to justify using powder material,” said Mike Littrell, president of CIDEAS Inc (buildparts .com). “This innovative material offers similar mechanical properties to polypropylene, high elongation, high impact and high recycling rate. We have a customer who frequently orders large, unique one-off parts that were not perfectly suited for a powder process. DuraForm PAx Natural is the perfect material to use for this type of application and build size while still being able to produce a beautifully finished product.”
Forward-looking statements
Certain statements made in this release that are not statements of historical or current fact are forward-looking statements within the meaning of the Private Securities Litigation Reform Act of 1995. Forward-looking statements involve known and unknown risks, uncertainties and other factors. which may cause the company’s actual results, performance or achievements to be materially different from historical results or any future results or projections expressed or implied by such forward-looking statements. In many cases, forward-looking statements can be identified by words such as “believes”, “believes”, “expects”, “may”, “will”, “estimates”, “intends”. , “anticipate” or “plan” or the negative of these terms or other comparable terms. Forward-looking statements are based on management’s current beliefs, assumptions and expectations and may include comments about the company’s beliefs and expectations regarding future events and trends affecting its business and are necessarily subject to uncertainties, including many are outside the company’s control. The factors described under the headings “Forward-Looking Statements” and “Risk Factors” in the company’s periodic filings with the Securities and Exchange Commission, as well as other factors, could cause actual results to differ materially from those reflected or anticipated in forward-looking statements. Although management believes that the expectations reflected in the forward-looking statements are reasonable, the forward-looking statements are not and should not be taken as guarantees of future performance or results, and they will not necessarily prove to be precise indications. the times at which these performances or results will be achieved. The forward-looking statements included are made only as of the date of the statement. 3D Systems and EMS Group assume no obligation to update or revise any forward-looking statements made by or on behalf of management, whether as a result of future developments, subsequent events or circumstances or otherwise, except if required by law.
About 3D Systems
Over 30 years ago, 3D Systems brought the innovation of 3D printing to the manufacturing industry. Today, as the leading additive manufacturing solutions partner, we bring innovation, performance and reliability to every interaction – enabling our customers to create products and business models never before possible. Through our unique offering of hardware, software, materials and services, each application-specific solution is powered by the expertise of our application engineers who work with customers to transform the way they deliver their products and services. 3D systems meet a variety of advanced applications in healthcare and industrial markets such as medical and dental, aerospace and defense, automotive and durable goods. More information about the company is available at www.3dsystems.com.
About EMS GRILTECH
The EMS Group, in which the Business Unit EMS-GRILTECH is incorporated, is an independent Swiss company with worldwide activities in the business areas High Performance Polymers and Specialty Chemicals. In the High Performance sector, we develop, manufacture and market high performance engineering plastics for demanding technical applications. In the area of specialty chemicals, we focus on high-quality additives, thermoplastic adhesives, fibers – and, latest addition, polymers specially designed and refined for the additive manufacturing industry. As technology leaders, we meet the highest quality requirements and strive to meet the individual requirements of our customers. More information about the company is available at www.emsgriltech.com.
A photo accompanying this ad is available at https://www.globenewswire.com/NewsRoom/AttachmentNg/10028753-5f25-4fec-9c7c-d15dc0d67eef
Investor Contact: investor.relations@3dsystems.com Media Contact: press@3dsystems.com Investor Contact: finance@ems-group.com Media Contact: media@ems-group.com